DMAIC and other Six Sigma Tools to Drive Continuous Improvement
Methodology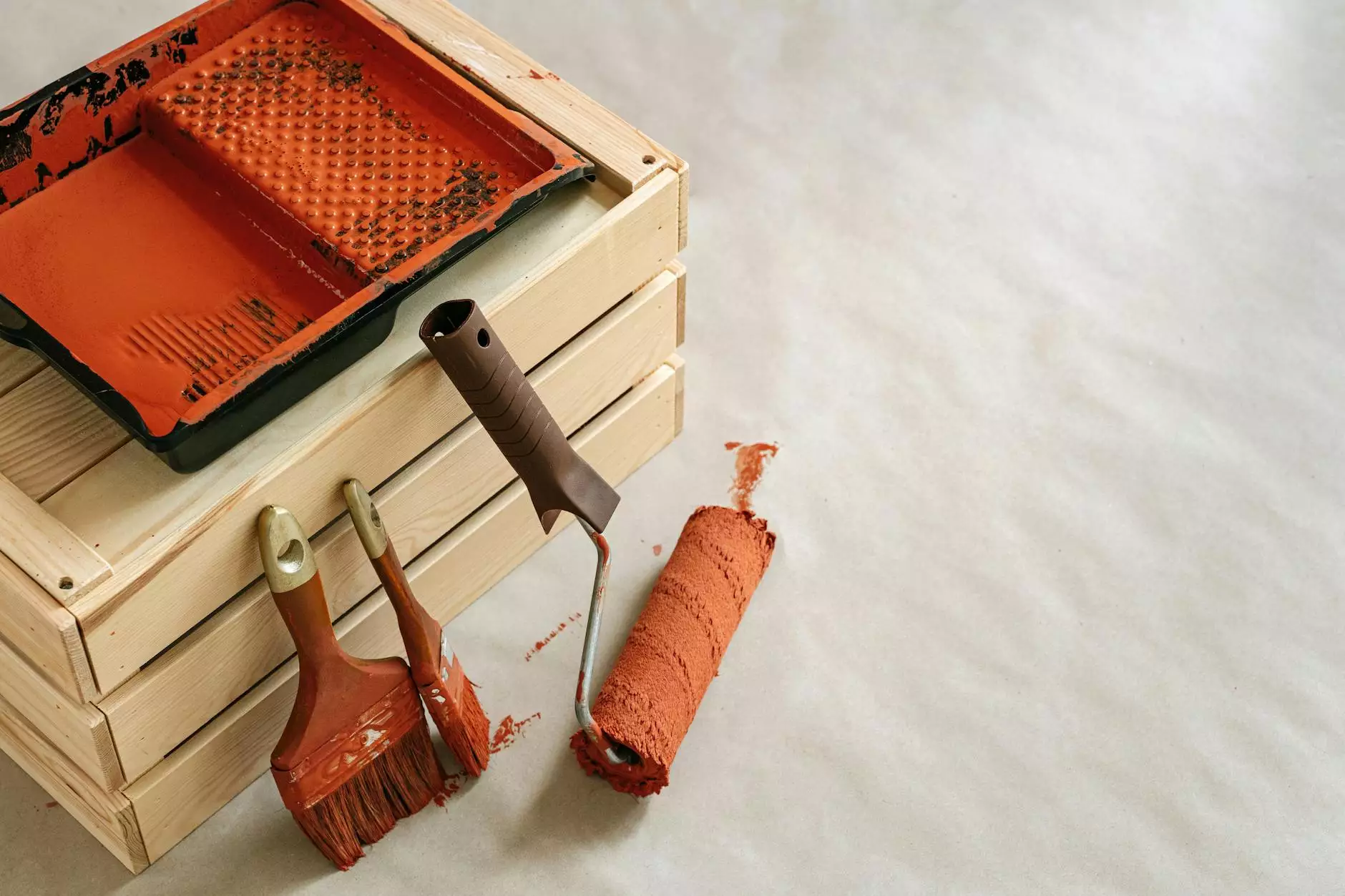
Introduction
Welcome to Graymatter SEO, your trusted partner in driving continuous improvement for your business. In this article, we will explore the power of DMAIC (Define, Measure, Analyze, Improve, Control) and other Six Sigma tools to optimize your business processes and enhance overall performance. With our exceptional SEO services, we assist businesses like yours to rank higher on search engines like Google, increasing visibility and attracting valuable traffic to your website.
The Importance of Continuous Improvement
In today's highly competitive business landscape, continuous improvement is crucial for sustainable success. Organizations that embrace a culture of continuous improvement consistently find ways to enhance efficiency, reduce waste, and deliver superior products and services to their customers. DMAIC and other Six Sigma tools provide a structured approach to identify and tackle process inefficiencies, enabling businesses to achieve higher levels of quality, productivity, and customer satisfaction.
Benefits of DMAIC and Six Sigma Tools
Implementing DMAIC and other Six Sigma tools offer numerous benefits for your business:
- Process Optimization: DMAIC provides a systematic framework to analyze and optimize existing processes, leading to increased efficiency and reduced errors.
- Data-Driven Decision Making: By collecting and analyzing data using Six Sigma tools, you gain valuable insights that guide informed decision making and improve overall business performance.
- Quality Improvement: Six Sigma methodologies focus on eliminating defects and reducing process variation, resulting in improved product or service quality and customer satisfaction.
- Cost Reduction: Identifying and eliminating waste within your processes can significantly reduce costs and improve your bottom line.
- Employee Engagement: Involving employees in continuous improvement efforts empowers them to contribute to process enhancements, fostering a culture of ownership and innovation.
Implementing DMAIC for Continuous Improvement
DMAIC is a widely recognized Six Sigma methodology used for continuous improvement. Let's dive into each step:
Define
The first step of DMAIC is to define the problem or opportunity for improvement. Clearly articulate goals, scope, and desired outcomes. By precisely defining the issue, you create a solid foundation for the subsequent steps.
Measure
Accurate measurement is crucial for data-driven decision making. In this step, collect relevant data and establish baseline performance metrics. Identify key performance indicators (KPIs) and ensure data integrity to enable accurate analysis.
Analyze
Analyze the collected data to identify patterns, root causes, and areas for improvement. Utilize Six Sigma tools such as fishbone diagrams, Pareto charts, and process flowcharts to visualize and understand the underlying issues affecting your processes.
Improve
Based on the analysis, develop and implement solutions to address the identified issues. Test and refine these solutions to ensure they effectively resolve the problem. Implementing change management strategies will aid in smooth transitions.
Control
The final step of DMAIC focuses on sustaining the improvements achieved. Define control mechanisms to monitor ongoing performance and establish processes to prevent regression. Regularly review and refine control measures to ensure continued success.
Other Six Sigma Tools
Beyond DMAIC, Six Sigma offers a range of powerful tools and methodologies to support your continuous improvement journey. These include:
- SIPOC (Suppliers, Inputs, Process, Outputs, Customers): A tool used to identify all the critical elements of a process, including stakeholders, inputs, and outputs.
- CTQ (Critical-to-Quality): Identifying and quantifying key metrics that directly impact customer satisfaction and business objectives.
- Hypothesis Testing: Statistically analyze sample data to validate or reject assumptions.
- Design of Experiments (DOE): Optimize process variables to achieve desired outcomes while minimizing waste and variation.
- Statistical Process Control (SPC): Monitor and control process performance using statistical methods.
Graymatter SEO: Driving Continuous Improvement and Business Success
At Graymatter SEO, we understand the importance of continuous improvement in achieving online success. Our team of dedicated professionals specializes in providing top-notch SEO services tailored to your business needs. By utilizing cutting-edge techniques and leveraging our expertise, we help you outrank your competitors on Google and attract valuable organic traffic to your website.
With a focus on comprehensive keyword research, content optimization, backlink building, and technical SEO, we ensure your website's visibility and authority steadily increase. We craft engaging and informative content that resonates with your target audience, keeping them on your website longer and driving conversions.
Partner with Graymatter SEO and experience the power of DMAIC and Six Sigma tools in driving continuous improvement for your online presence. Contact us today to learn more about our services and how we can help your business thrive in the competitive digital landscape.
Conclusion
DMAIC and other Six Sigma tools provide a structured approach to driving continuous improvement in your business processes. Implementing these methodologies enables you to optimize efficiency, enhance quality, and reduce costs. With Graymatter SEO's industry-leading SEO services, you can supercharge your online presence, outrank your competitors, and attract your target audience to drive business growth. Embrace continuous improvement with Graymatter SEO today!