The State of Plastic Molding in China: A Comprehensive Overview
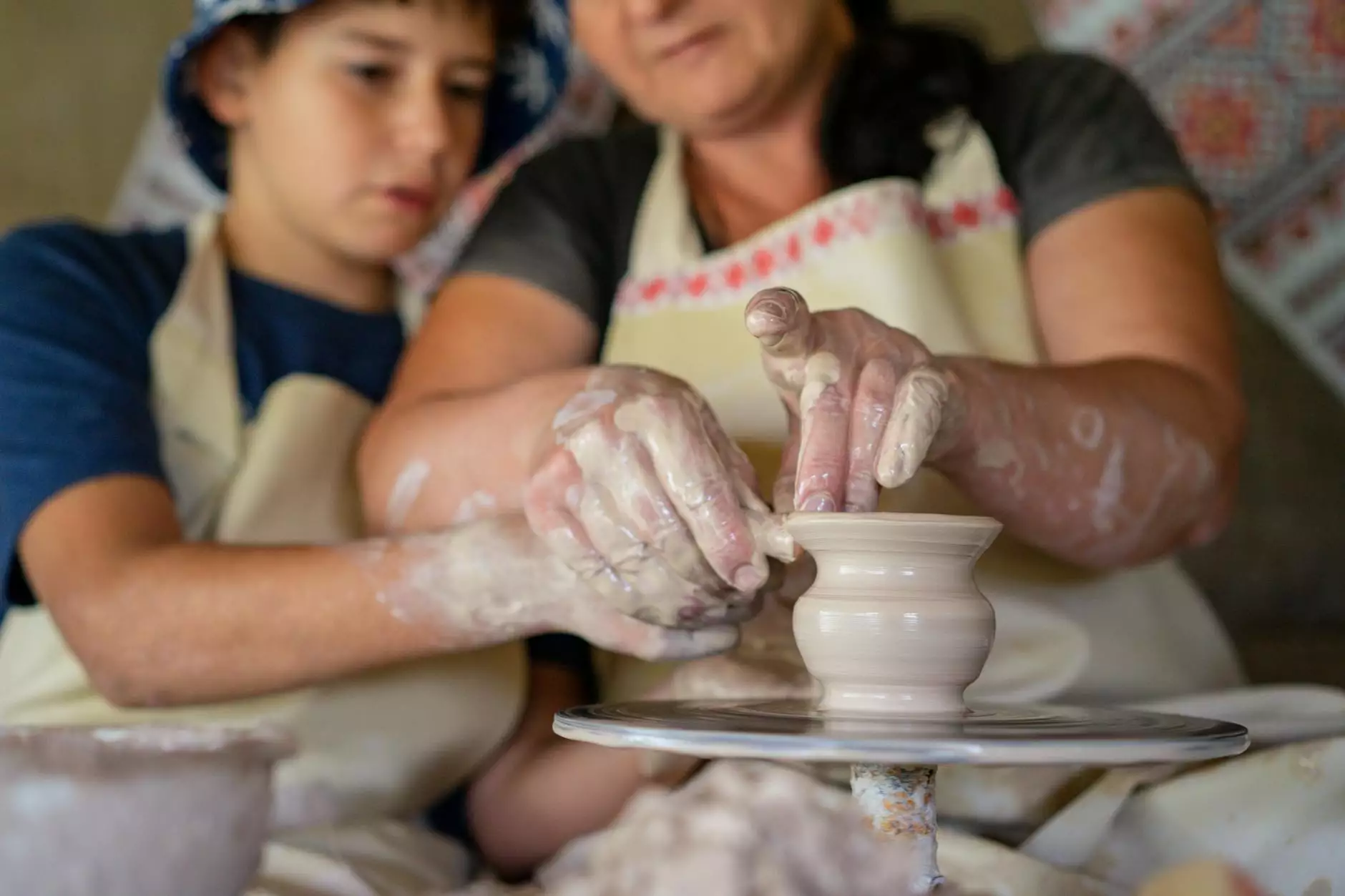
The plastic molding industry in China has transformed into a global powerhouse, characterized by innovation, efficiency, and extensive manufacturing capabilities. This detailed article delves into the intricacies of plastic molding in China, with particular emphasis on plastic mold makers and plastic injection mould manufacturers. By understanding the various components of this thriving sector, stakeholders can better position themselves to take advantage of the opportunities it presents.
Understanding Plastic Molding
Plastic molding is a manufacturing process that involves shaping liquid plastic into specific forms through the use of molds. It is a preferred method for producing large quantities of identical parts, making it indispensable in industries such as automotive, consumer goods, electronics, and more. The main categories of plastic molding include:
- Injection Molding: The most common form that injects molten plastic into a mold.
- Blow Molding: Typically used for hollow objects like bottles.
- Compression Molding: Suitable for rubber and thermosetting plastics.
- Rotational Molding: Used for producing large, hollow parts.
The Advantages of Plastic Molding in China
China has established itself as a leader in the plastic molding domain due to various strategic advantages:
1. Cost-Effectiveness
One of the most significant benefits of plastic molding in China is the competitive pricing. The country offers lower labor costs and well-established supply chains that reduce overhead expenses. This affordability attracts businesses from all over the globe looking to manufacture products at a lower cost without sacrificing quality.
2. Advanced Technology and Expertise
Chinese plastic mold makers leverage cutting-edge technology and utilize computer-aided design (CAD) and computer-aided manufacturing (CAM) systems. This results in precision manufacturing capabilities that are essential for producing complex molds and components. The country also boasts a workforce skilled in advanced manufacturing techniques, continually enhancing their expertise through training and development programs.
3. Vast Production Capacity
China's manufacturing environment is characterized by its vast production capacity, which enables companies to meet large-scale orders efficiently. This capacity is crucial for businesses that require a quick turnaround on their products, as the speed of production can significantly impact time-to-market.
The Role of Plastic Mold Makers
Plastic mold makers are the backbone of the plastic molding industry, responsible for creating the molds utilized in the manufacturing process. The process can be broken down into several key stages:
1. Design and Prototyping
Plastic mold makers begin by designing custom molds tailored to the specifications of the client. This phase often involves creating tangible prototypes, ensuring that the client's requirements are met before full-scale production begins. Prototyping is vital for identifying potential issues and refining the product design.
2. Construction and Production
Once the mold design is approved, mold makers proceed to construct the molds. This process involves various techniques, including machining and assembly, ensuring high precision. The quality of the mold is imperative, as it directly affects the final product's integrity.
3. Testing and Quality Assurance
Before the molds are put into production, thorough testing is conducted to ensure they function correctly and produce parts within specified tolerances. Quality assurance is essential in the plastic molding industry to maintain high standards and meet client expectations.
The Role of Plastic Injection Mould Manufacturers
Plastic injection mould manufacturers play a crucial role in transforming raw plastic materials into finished products through the injection molding process. Their responsibilities encompass the following:
1. Material Selection
Injection mould manufacturers must select the appropriate plastics based on the application and desired characteristics of the end product. Materials such as ABS, polycarbonate, and polypropylene are popular choices, each offering unique properties suited to various industries.
2. Injection Molding Process
The core of their function is executing the injection molding process, where the selected plastic is heated until molten and injected into the mold under pressure. This ensures that the mold is filled efficiently, allowing for accurate replication of parts.
3. Post-Processing and Finishing
After the parts have cooled and solidified, they undergo post-processing, which may include trimming, surface finishing, and assembly. These steps ensure that the final product meets both functional and aesthetic requirements.
Quality Control in Plastic Molding China
Maintaining high-quality standards is vital for plastic mold makers and injection mould manufacturers in China. Several measures are employed to ensure product quality:
- ISO Certification: Many manufacturers strive for ISO certification, demonstrating their commitment to quality management practices.
- Regular Inspections: Routine inspections are conducted throughout the production process to identify any defects early and rectify them promptly.
- Client Feedback: Manufacturers often seek feedback from clients to continuously improve their processes and products.
Environmental Considerations in Plastic Molding
As global awareness of environmental issues grows, the plastic manufacturing industry must adapt to more sustainable practices. The Chinese government and manufacturers are increasingly focusing on environmentally friendly practices, including:
1. Recycling Initiatives
Many companies are implementing recycling programs, not only for waste management but also to leverage recycled plastics in their production processes. This commitment helps reduce the consumption of raw materials and minimizes environmental impact.
2. Advances in Bioplastics
Innovation in bioplastics offers an alternative to traditional petroleum-based plastics. Manufacturers are researching and using bioplastics derived from renewable resources, reducing the reliance on fossil fuels and decreasing carbon footprints.
3. Energy Efficiency
Investing in energy-efficient machinery and production techniques is becoming a priority for many manufacturers. Utilizing renewable energy sources, such as solar or wind power, contributes to a more sustainable operation overall.
Global Competitiveness of Chinese Plastic Molding
The Chinese plastic molding industry faces competition from other global players; however, its ability to innovate and adapt ensures it remains competitive. Key factors contributing to its competitiveness include:
- Innovation: Continuous improvement in technologies and processes keeps Chinese manufacturers at the forefront of the industry.
- Strategic Partnerships: Collaborations between manufacturers, suppliers, and research institutions foster innovation and enhance capabilities.
- Diverse Market Reach: China's plastic molding sector serves various industries globally, which helps mitigate risks associated with market fluctuations.
Conclusion: The Bright Future of Plastic Molding in China
To summarize, the plastic molding industry in China is well-positioned for continued growth. With advantages such as cost-effectiveness, advanced technology, and vast production capacities, China remains a leader in the global market. As the industry evolves, focusing on innovation, quality control, and sustainability will be critical for maintaining this competitive edge. Business owners and stakeholders looking to leverage the benefits of plastic molding should consider partnering with established and reputable plastic mold makers and plastic injection mould manufacturers like hanking-mould.com, ensuring access to high-quality products and services.