Understanding the **Three Valve Manifold**: Your Comprehensive Guide
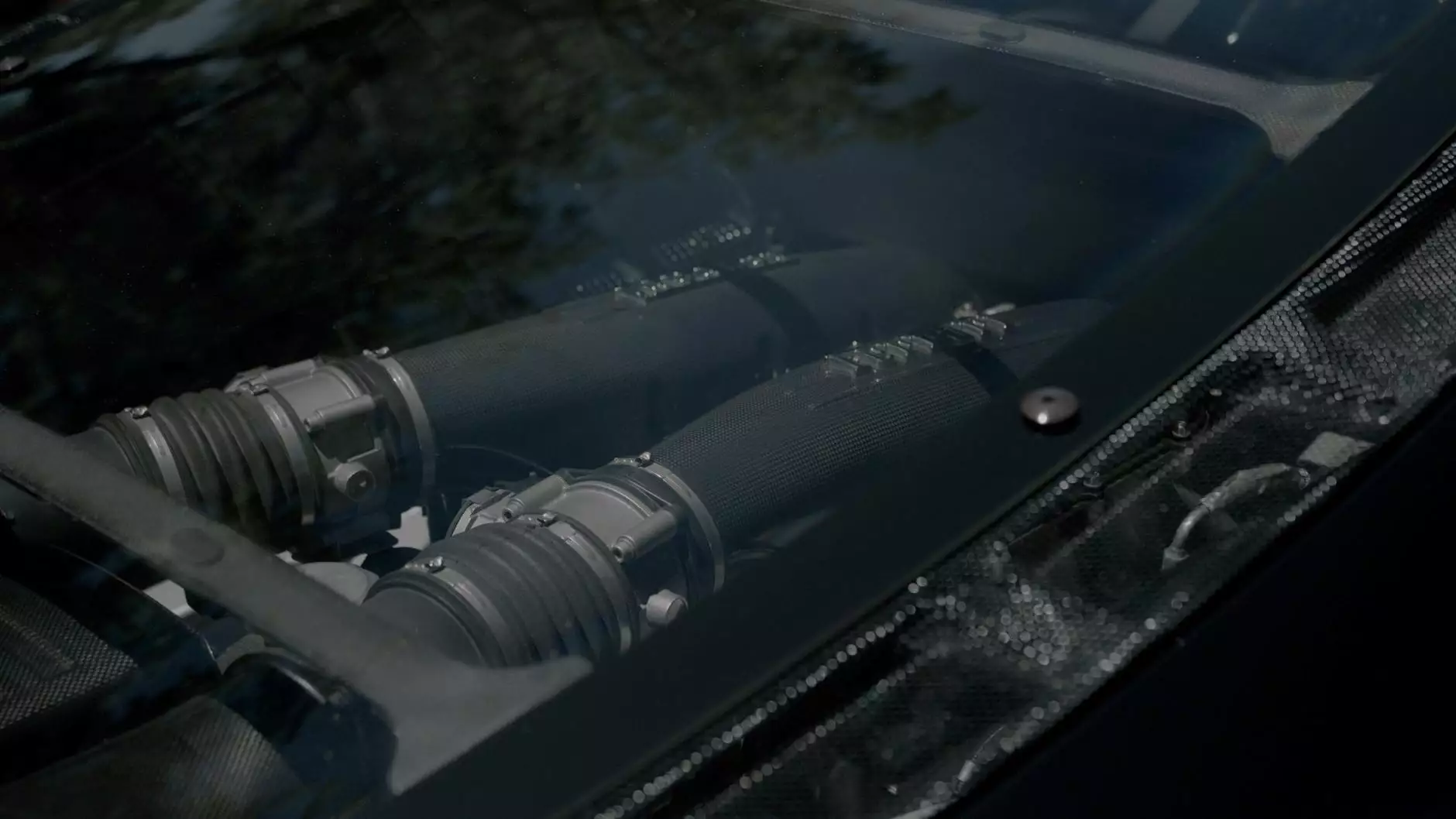
The three valve manifold is an essential component in various industrial applications, particularly in the field of fluid control systems. This article will provide an in-depth exploration of the three valve manifold, covering its design, functionality, applications, and relevance in sectors such as oil and gas, chemical processing, and instrumentation. By the end of this article, you will have a thorough understanding of this crucial fitting and its role in ensuring system efficiency.
What is a Three Valve Manifold?
A three valve manifold is a device that integrates three separate valves into one compact assembly. These valves typically include:
- Block Valve: Used to isolate the manifold from the line.
- Bleed Valve: Allows for safe venting of pressure within the system.
- Equalizing Valve: Balances the pressure across different sections of the manifold.
This configuration allows for efficient management of fluids, making the three valve manifold widely employed in tube fittings, ferrule fittings, and other piping systems.
Key Features of the Three Valve Manifold
Some of the primary features that define a high-quality three valve manifold include:
- Compact Design: The integration of three valves into a single location saves space and reduces the complexity of pipe systems.
- Durability: Made from robust materials that withstand high pressures and harsh environments, they are ideal for industrial applications.
- Safety: Properly designed manifolds contain safety features that minimize the risk of leaks and pressures accidents.
- Ease of Installation: Typically come with straightforward installation instructions, ensuring quick and simple setup.
- Versatility: Compatible with various tube sizes and fittings, making them adaptable to different systems.
Applications of the Three Valve Manifold
The versatility of the three valve manifold makes it suitable for a wide range of applications, including:
1. Oil and Gas Industry
In the oil and gas sector, three valve manifolds are crucial for connecting pressure transmitters to the piping system, allowing accurate pressure measurements and system monitoring. Their role in isolating and venting pressure ensures both operational efficiency and safety.
2. Chemical Processing
In chemical plants, the ability to manage and control fluid flow without extensive piping modifications is vital. The three valve manifold facilitates precise pressure control and allows operators to quickly bleed off pressure, maintaining a safe working environment.
3. Instrumentation Systems
Instrumentation applications benefit from the three valve manifold's compact design, which simplifies installations while providing reliable connections to sensors and transmitters. This is particularly important in environments where space is limited, yet functionality cannot be compromised.
4. Water Treatment Facilities
In water treatment plants, the need for effective monitoring and control of fluid processes is paramount. Three valve manifolds are employed to ensure efficient operation of various instruments measuring water quality parameters.
Understanding How a Three Valve Manifold Works
To fully appreciate the utility of a three valve manifold, it’s beneficial to understand how each valve operates within the system:
Block Valve
The block valve is primarily responsible for isolating the downstream equipment or pipe from the manifold system. When closed, it prevents fluid flow, allowing for maintenance or safety checks without affecting the entire system.
Bleed Valve
The bleed valve ensures that any trapped pressure within the manifold can be safely vented. This is particularly important in preventing pressure build-up that could lead to system failures or dangerous situations during maintenance operations.
Equalizing Valve
The equalizing valve works to balance the pressure in different parts of the manifold. This is crucial when dealing with measurements from multiple systems, ensuring that accurate readings are maintained without complications from pressure variances.
Maintenance and Troubleshooting of the Three Valve Manifold
Regular maintenance is essential to ensure that the three valve manifold continues to operate effectively. Here are some best practices:
- Regular Inspections: Periodically check for leaks, corrosion, and physical damage.
- Functional Testing: Regularly assess the functionality of each valve to ensure they operate correctly.
- Cleaning: Keep the manifold and surrounding area clean to prevent contaminants from affecting the system.
- Replacing Seals and Gaskets: Over time, seals and gaskets can wear out. Regularly checking and replacing them can prevent leaks.
Choosing the Right Three Valve Manifold for Your Needs
Selecting the appropriate three valve manifold involves considering various factors:
- Material: Choose materials suitable for your specific applications, considering factors such as fluid compatibility and environmental conditions.
- Pressure Rating: Ensure that the manifold's pressure rating meets or exceeds the requirements of your system.
- Size and Configuration: Depending on your installation needs, assess the size and valve configuration that aligns with your pipe fittings.
Conclusion
In conclusion, the three valve manifold is a crucial element in many industrial applications, providing a compact solution to fluid management challenges. Its unique features enable effective pressure control, safety, and efficiency in systems across various sectors, including oil and gas, chemical processing, and more. By understanding its components and applications, businesses can leverage the three valve manifold to enhance their operational capabilities.
For high-quality tube fittings, forged pipe fittings, manifold valves, and more, visit us at TechTubes.in to explore our extensive range of products that meet the needs of your industry.